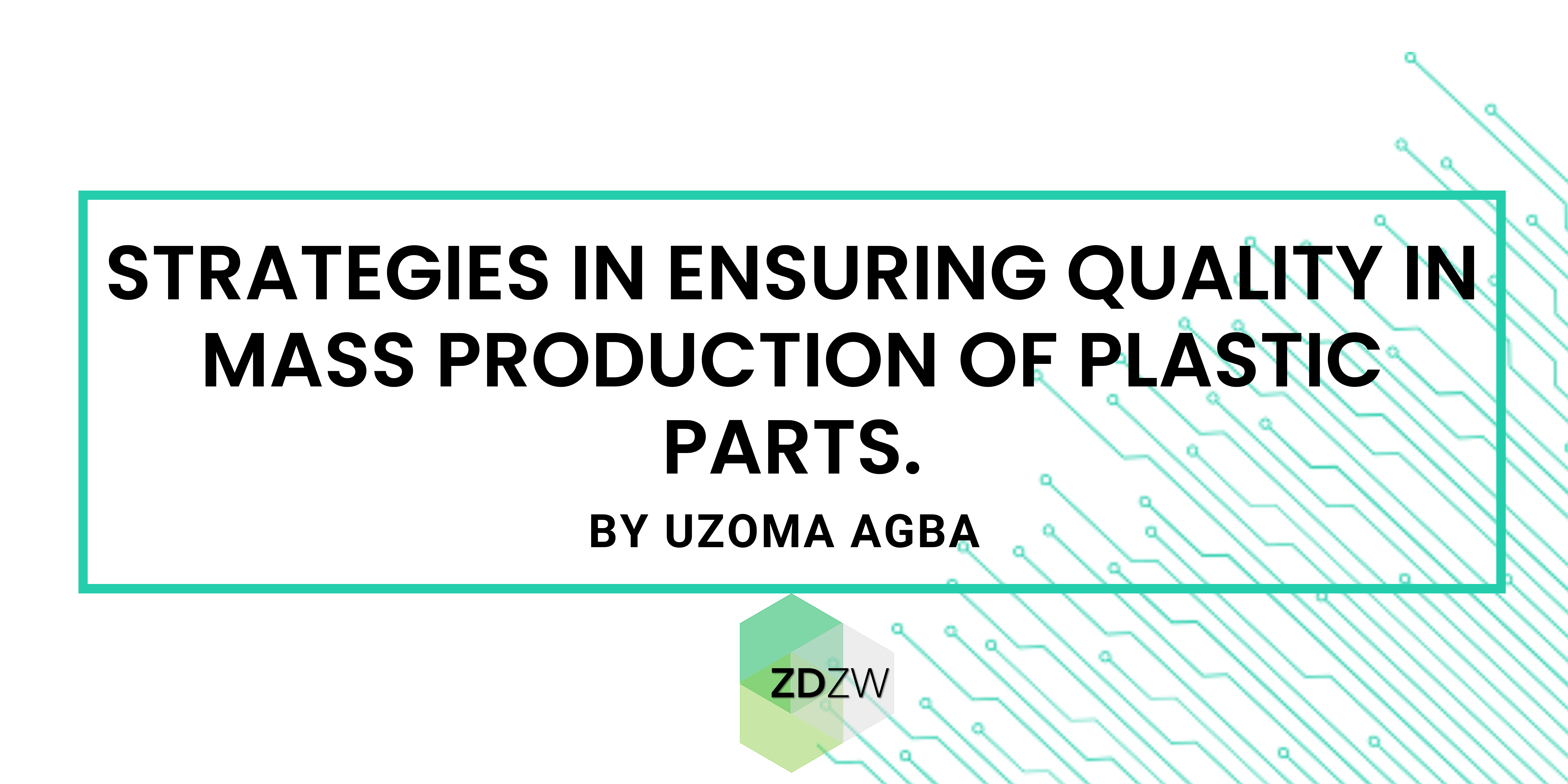
Strategies in ensuring quality in mass production of plastic parts.
For all those interested in exploring the vital role of quality assurance in plastic manufacturing, which emphasizes its impact on product reliability, customer satisfaction, and regulatory compliance, this article by Uzoma Agba, ZDZW project Ambassador, explores these areas in depth. It also outlines challenges such as defect detection and environmental influences while detailing strategies like quality planning, control, and improvement. The article introduces the innovative ZDZW project, aiming to revolutionize plastic production through smart technologies and sustainability. It highlights expected outcomes, including reduced waste and enhanced productivity, emphasizing the importance of holistic approaches for sustainable and socially responsible manufacturing practices.
Strategies in ensuring quality in mass production of plastic parts.
In the contemporary manufacturing landscape, the mass production of plastic parts plays a pivotal role across various industries, including automotive, electronics, consumer goods, and healthcare. The reliability and quality of these plastic components are paramount to meeting safety standards, maintaining product integrity, and safeguarding brand reputation. This article delves into the strategies and best practices for quality assurance in the mass production of plastic parts, with a particular focus on the innovative Zero Defects Zero Waste (ZDZW) approach.
Quality Assurance in Plastic Manufacturing
Quality assurance (QA) is a comprehensive set of processes, practices, and activities implemented in manufacturing to ensure that production meets the highest quality standards. From design and raw material selection to manufacturing processes, inspections, and product distribution, every aspect falls under the umbrella of Quality Assurance .
Why Quality Assurance (QA) matters
Quality assurance in manufacturing is crucial for several reasons:
First, it ensures that products are reliable and meet performance standards. This means customers can trust that the products they receive will work as expected.
Secondly, quality assurance maintains customer satisfaction by ensuring that customers get high-quality products that meet their expectations. When customers are happy with the products they receive, it builds trust and loyalty to the brand.
Manufacturers also implement Quality Assurance to comply with standards, regulations, and safety requirements. Meeting these standards helps companies achieve certifications and fulfill legal obligations, ensuring they operate within the law.
Moreover, Quality Assurance helps identify deviations in raw materials and minimizes product defects. By catching these issues early on, manufacturers can reduce scrap production and cut costs.
Challenges in Quality Assurance
- Defect Detection & Analysis: Visual inspections for defect detection can be challenging, especially for complex parts with intricate geometries. Meticulous checks are essential, as even skilled inspectors may miss subtle defects.
- Process Stability & Deviations: Batch-to-batch deviations and variations in raw materials can impact final part quality. Monitoring processes in real-time is challenging, leading to difficulties in implementing prompt reactions to deviations.
- Environmental Influences: Temperature, humidity, and other environmental factors affect material behavior, potentially leading to defective parts. Controlling contamination in production environments also poses challenges.
- Quality Assurance Inspections: QA inspections before and after processing may be unreliable, and the quality sampling technique has limitations and is cost-intensive.
Steps Involved in Quality Assurance
Quality assurance is a systematic process that ensures products meet necessary quality standards throughout the manufacturing process.
The Key Steps Include:
- Quality Planning: Setting quality objectives, identifying processes, defining standards, identifying resources, and developing a quality plan.
- Quality Control: This involves monitoring and controlling the production process to ensure that the final products meet the specified quality standards. It includes inspection, testing, and validation processes to identify and correct deviations from the set standards.
- Quality Improvement: Continuous improvement is crucial for maintaining and enhancing quality in manufacturing. Regular reviews, feedback mechanisms, and implementation of corrective actions based on data analysis contribute to ongoing quality enhancement.
- Quality Training: Ensuring that all personnel involved in the manufacturing process are adequately trained in quality procedures and standards is essential. This step contributes to a culture of quality consciousness within the organization.
- Quality Assessment: Regular assessments and audits help evaluate the effectiveness of the quality assurance processes. This step ensures that the established standards are consistently met and identifies areas for further improvement.
The ZDZW Project and Sustainability in Plastic Production
The ZDZW project introduces an innovative approach, incorporating smart technologies like Non-Destructive Inspection (NDI) to minimize defects, reduce waste, and optimize resource consumption in plastic production. This approach revolutionizes manufacturing by combining innovation and sustainability.
To achieve quality in plastic production, projects must address the three pillars of sustainability:
- Life Cycle Assessment (LCA)
- Life Cycle Cost (LCC)
- Social Impact Assessment (SIA).
Life Cycle Assessment (LCA)
LCA evaluates the ecological footprint of products or processes throughout their life cycle, from raw material extraction to disposal. By measuring resource consumption and environmental impacts, manufacturers can identify areas for improvement and optimize their value chain. This not only enhances sustainability but also serves as a unique selling point for gaining customer trust.
Life Cycle Cost (LCC)
LCC assesses the financial implications of a product’s life cycle, including acquisition, operation, maintenance, and disposal costs. By considering environmental costs alongside financial expenses, companies can make informed decisions that balance sustainability and profitability.
Social Impact Assessment (SIA)
SIA evaluates the social consequences of projects or interventions to minimize harm and maximize benefits for society. In the context of plastic production, SIA focuses on workforce impact, including job creation, upskilling opportunities, and technology integration. Collaborative approaches involving workers ensure that projects align with stakeholder needs and facilitate technology acceptance.
Why Quality Control Checks Matter In Plastic Injection Molding
Plastic injection molding quality engineering is crucial for project success. Without established molder quality control checks, manufacturers may encounter issues such as:
Changes in Materials:
Injection molding plastic supplier specifications don’t always provide a complete understanding of plastic performance. This can lead to mid-production material modifications or even scrapping the entire run. Seeking input from an experienced injection molder is crucial for proper plastics selection.
Redesign for defect correction:
Starting production only to discover a catastrophic design flaw or delivering defective products can be complicated, brand-damaging, and wasteful. Mold experts, especially those well-versed in Design for Manufacturability (DfM), can detect and correct defects early in the design phase, avoiding production or public issues.
Too many secondary operations:
While secondary operations can enhance injection molded part quality, excessive additions may compromise product quality, performance, and shelf appeal. Working with a molder can offer streamlined solutions like over molding, combining parts and materials into a single product for better quality management.
Production delays:
Lack of guidance from an injection molder throughout a project increases the risk of compromised part quality and production delays. Expert scientific molding engineers can identify and optimize efficiencies, ensuring consistent repeatability across machines, operators, lines, and runs, minimizing the risk of delays.
Furthermore, employing a plastics quality control test is essential for several reasons:
Ensuring product quality:
Quality control tests guarantee that plastic products meet required specifications, promoting consistency, customer satisfaction, and repeat business.
Reducing waste:
Identifying defects early in the manufacturing process through quality control tests allows timely correction, reducing waste, and saving resources.
Improving efficiency:
Quality control tests monitor the manufacturing process, identifying areas for improvement, enhancing efficiency, and reducing production time and costs.
Meeting regulatory requirements:
Quality control tests ensure plastic products comply with regulatory standards, such as FDA food contact regulations, meeting industry requirements.
Maintaining brand reputation:
Poor product quality can damage a company’s reputation. Quality control tests safeguard brand reputation and maintain customer trust by ensuring product consistency and quality.
Visual inspection:
This is a common practice in plastic manufacturing that involves visually examining products to ensure they meet quality standards. Inspectors may use tools like magnifying glasses and gauges to aid the process. Visual inspection is crucial for identifying defects such as surface blemishes, dimensional errors, and color variations. It is especially important for products with aesthetic or strict dimensional requirements, ensuring they meet customer expectations. Performing effective visual inspection ensures high-quality products and serves as a critical step in the manufacturing process.
In plastic extrusion, for example, the visually inspected extruded product identifies surface defects like bubbles or scratches, ensuring optimal appearance and performance.
Goals and expected outcomes from implementing the ZDZW approach
The goal of ZDZW is to find a more efficient, cost-effective, and agile system to carry out the visual and dimensional inspection of thermoplastics parts processed by injection moulding. The expected outcomes include inspecting 100% of produced parts, significantly reducing scrap, improving the use of raw materials, and reinforcing the quality standards of delivered products.
The anticipated improvements will include a decrease of 9-12% in energy consumption, 8-12% in greenhouse gas emissions, and 2-3% in waste and rejection rates. Simultaneously, productivity is expected to increase by 7-10%, leading to global savings of 3-5%.
The proposed solution is the ZDZW Visual Inspection Suite, a comprehensive approach to achieve these ambitious goals.
The role of quality control tests in plastic manufacturing
Using quality control tests for plastics is vital for several reasons, including ensuring product quality, reducing waste, improving efficiency, meeting regulatory requirements, and maintaining brand reputation.
Visual inspection in plastic manufacturing
Visual inspection is a common and essential type of inspection in plastic manufacturing. It involves visually examining the finished product to identify surface defects, ensuring it meets necessary quality standards.
Conclusion
In conclusion, quality control in plastic manufacturing is not merely about adhering to industry standards but involves understanding the material nuances, continuous process refinement, and a commitment to excellence.
The ZDZW project, with its focus on sustainability and smart technologies, exemplifies an approach that can lead the industry towards a more sustainable and socially responsible future. Enhancing quality in plastic production requires a holistic strategy, integrating advanced technologies, conducting comprehensive assessments, and fostering collaboration for long-term success and minimal environmental impact.
Through initiatives like ZDZW, plastic production can contribute significantly to a sustainable and socially responsible future across diverse industries and processes.
About the author
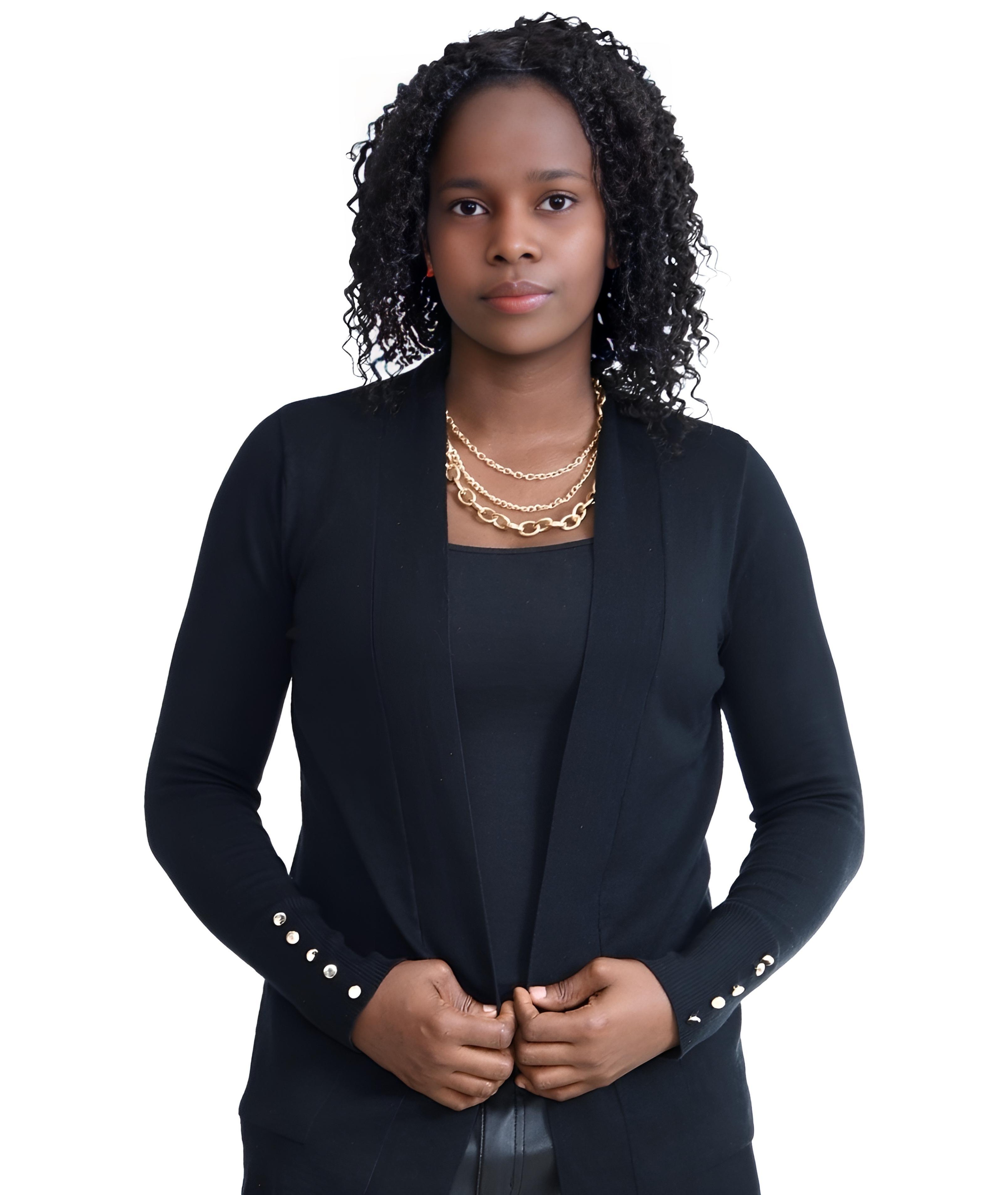
Uzoma Agba is a Business Tech Professional and a Startup Advisor associated with Seedstars, Techstars, Google for Startups, Google Hustle Academy, and serves as a Domain Expert with Carbon 13. Her expertise encompasses various sectors, including Smart Manufacturing, Fintech, Health, Agriculture, Digital Startups, Startup Education, Tech Hubs, Social Impact, and Media in Europe.
Uzoma’s experience is evident in B2B and B2C domains, covering business development, sales, marketing, product design, and product management across different accelerator and incubator programs. Dedicated to creating impact-driven solutions, they focus on benefiting professionals, corporate organizations, and startups.