The use of AI in procurement planning revolutionizes industrial supply chain management. These algorithms, integrated into advanced software tools, consider a wide range of factors, including the production plan, material availability, lead times and the capabilities of multiple suppliers.
By analyzing historical data and anticipating new situations, these systems can accurately forecast the best supplier for each material, maximizing efficiency and minimizing costs. In addition, by continuously adapting and evaluating special offers and volume discounts, these solutions enable companies to optimize their procurement operations, gaining a crucial competitive advantage in the marketplace.
The Impact of Procurement on Production
Within the framework of the European AIDEAS project, the SOA (Applied Optimization Systems) group of ITI is developing AI algorithms to assist in the procurement planning and calculation of the procurement plan.
Product purchases within an industrial environment have, although it may not seem so, a great influence on manufacturing. On the one hand, purchases of raw materials and other materials, along with the purchase of resources of all kinds have a direct influence on production costs, if cheaper materials can be purchased, the cost of production decreases.
In addition to this, the timing of the purchase and the travel time of the products from the suppliers also affect when the materials will be available for production, i.e. they can directly affect the production plan and the production itself. A clear example of this would be when certain materials are missing and our only supplier is two months behind schedule, this implies that production will have to be shut down for two months.
Developing the AIDEAS Procurement Optimiser (AI-PO)
As mentioned above, the purchasing plan has a direct relationship with the production planning and the production itself. For this reason, in this project we developed a software tool (or application) that is able to perform the calculation of the procurement plan by using algorithms based on artificial intelligence.
This sourcing plan will not only take into account the current production plan, which defines the future material requirements, but also the existence of multiple suppliers for materials with different product delivery capacities, offers and prices for different batch sizes.
In addition to considering the current production plan and future availability of materials, our artificial intelligence algorithm considers the individual capabilities of suppliers. Each supplier has its own lead time, which can vary depending on transport mode and geographical location, stock availability and logistical efficiency. These lead times are critical to ensure that materials arrive in time to meet production deadlines.
Another crucial aspect this algorithm addresses is the maximum production capacity of each supplier. Although a supplier may offer more competitive prices, if it cannot meet the required demand in the necessary time, it could lead to production delays and ultimately to additional costs. Therefore, it is essential to find a balance between the cost of materials and the suppliers’ delivery capacity.
The AIDEAS project also emphasizes interoperability between different solutions developed in-house as well as with third party software. In this aspect, the necessary tools are provided so that AI-PO (Procurement Optimiser) can obtain production-related data from other solutions such as AI-FO or from the company’s own ERP where it will operate.
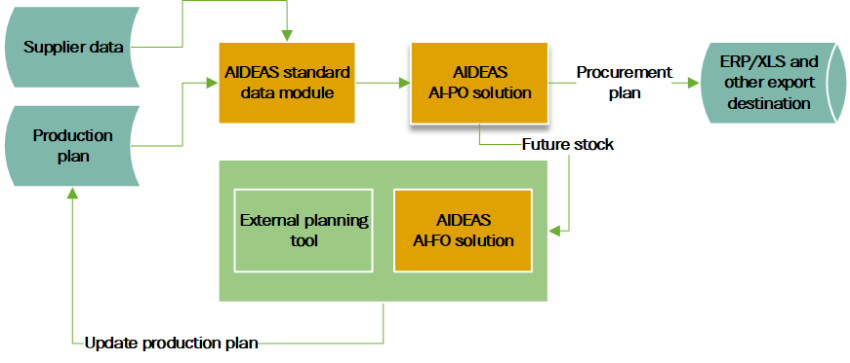
Figure 1- AIPO interaction with environment
Solution description
The AI-PO solution developed in this project uses advanced machine learning techniques to analyse large amounts of historical data, such as past orders, delivery times and price variations. With this information, the algorithm accurately selects the best supplier for each material at any given time. In addition, the algorithm is able to adapt to new situations as they arise, continuously maintaining its accuracy and efficiency.
An innovative aspect of our approach is the ability to consider special offers and volume discounts offered by suppliers. By evaluating different lot sizes and unit prices, the algorithm can determine the most cost-effective combination that meets production requirements. This allows companies to make the most of their financial resources and obtain a higher return on investment in their procurement operations.
Conclusion
The use of AI in procurement planning represents a significant advance in supply chain optimisation. By taking into account multiple factors such as production plan, material availability, lead times and supplier capabilities, these tools can help companies reduce costs, improve efficiency and ensure operational continuity. In a competitive environment where every advantage counts, implementing these solutions can make the difference between business success and failure.
Want to keep discussing this? Join the AIDEAS community and connect with over 2500 researchers, manufacturers and organizations from all over Europe.