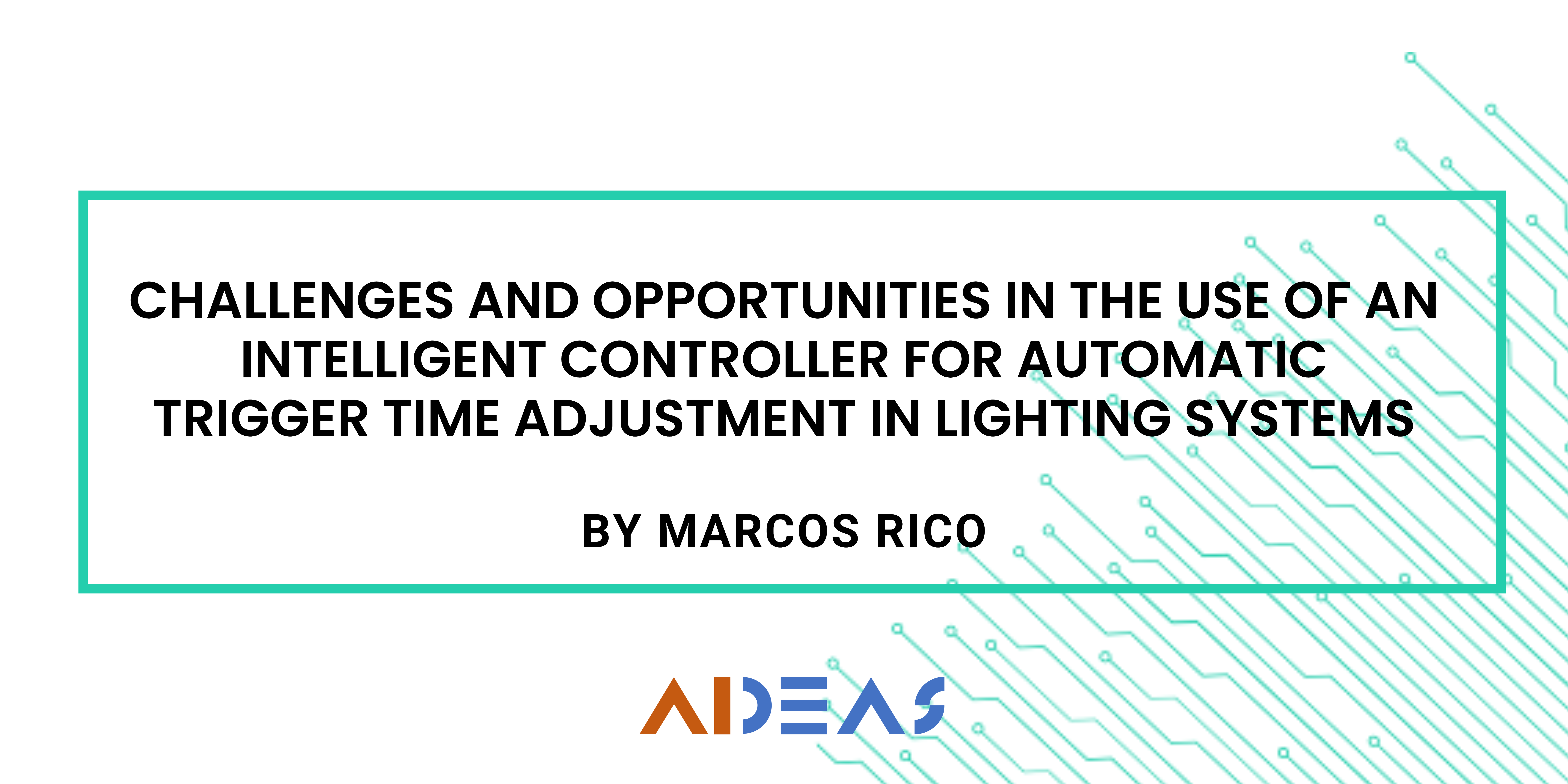
Challenges and opportunities in the use of an intelligent controller for automatic trigger time adjustment in lighting systems
The evolution of the operational context of companies in today’s market is marked by the strong influence of the Industry 4.0 concept. This fourth industrial revolution is enabling new perspectives in the way of working within a company, boosting its technological infrastructure based on a series of enablers. These enablers, among others, are:
- Big Data.
- Artificial Intelligence.
- Internet of Things.
- Autonomous robots.
- Additive manufacturing.
They all have one characteristic in common, and that is that they need data to function. The Internet of Things is the enabler that is mostly in contact with the real world and therefore with raw data. It is other enablers, such as autonomous robots or AI, that will use the data, once it has been prepared for exploitation, for operational development.
Within the framework of the development of solutions for the classification and inspection of products in the agricultural sector, this Industry 4.0 concept, together with its various enablers, can be applied to a multitude of tasks. Therefore, this paper aims to focus the scope of study on the analysis of the challenges and opportunities caused and enabled by Industry 4.0 and its application for a specific use case, which is based on the loss of the intensity level of the RGB and near-infrared gradient as a function of the temperature increase of the lighting system.
With this in mind, and Artificial Intelligence being the main enabler of the solution to be proposed, the work proposal consists of the design of an intelligent controller that is capable of self-adjusting the lighting trigger time depending on the temperature of the system in order to maintain the expected intensity level of the wavelengths with which the machines must operate during product inspection. This initially raises a number of concerns that present themselves as potential application challenges.
The first challenge stems from the need to work with different wavelengths of the electromagnetic spectrum, which can make the learning curve of the controller very difficult. The second challenge arises from the complexity of measuring the loss of light intensity over time, as it is necessary to have a non-time-varying element as a reference point for the analysis. This is because the product cannot be taken as a basis for this analysis given the high variability that can characterise it and, therefore, the wide range of colours (in terms of nanometers within the spectrum) that it can offer within the same variety. The last of the challenges inferred from the proposal described is the need to adapt the intelligent controller to different machines with different types of lighting methods (direct vs. diffuse) and different numbers of LEDs in their system.
However, the opportunities for improvement that arise from the use of AI (in this case through the intelligent controller) in the company’s operational framework are unquestionable. In the first place, its use can lead to a significant reduction in costs in the design of each of the machines. This is due to the fact that with the use of the controller it would be possible to eliminate one of the two thermal protection mechanisms against heat that are installed in all the equipment in order to avoid not only overheating but also the problem of gradient fading. Specifically, this is the cooler kit that provides liquid water to the circuit that cools the lighting system. In parallel, a stainless-steel structure is used to cover the LED boards as a heat sink. With the ability of the controller to adjust the trigger time of the illuminations to keep the intensity level of the RGB and near-infrared gradient stable at all times, it would be possible to dispense with the cooling kit having empirically proven that the temperature is controllable only with the steel structure. The cost reduction through the application of AI in this task would be 3.21% per machine.
Secondly, there is an opportunity to improve efficiency during inspection. Currently, despite having controlled the temperature of the lighting system, certain peaks can occur at specific times that lead to the sorting of products being carried out at a different intensity of the spectrum than expected, which can lead to undesirable results. With this new autotuning system, the efficiency of the process would be guaranteed throughout the life of the machine.
Finally, the possibility of automatically adapting the trigger time would also reduce the supervisory work during the inspection process and make it almost completely autonomous.
In conclusion, it is undeniable that Artificial Intelligence forms part of one of the fundamental pillars of the new industrial revolution that surrounds the business world, and its implementation in the operations of any company brings with it the appearance of multiple challenges of high complexity but with the guarantee of obtaining great competitive advantages given its heterogeneous capabilities within any environment.