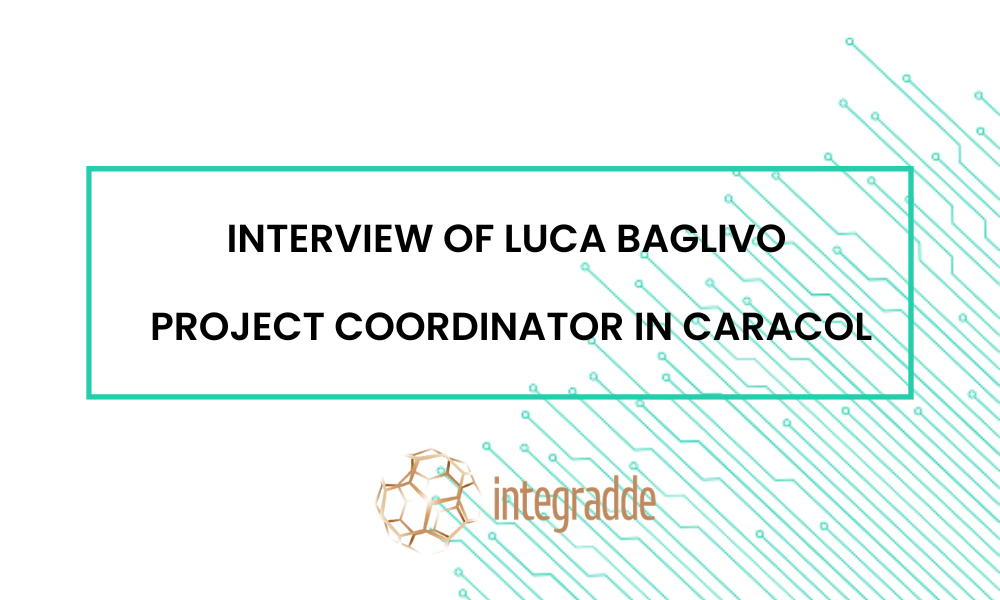
Interview of Luca Baglivo - Project Coordinator in CARACOL
Could you please give our audience a description of your company?
Caracol was born from the idea of pushing the limits of AM, beyon what was possible. We brought that idea to life by evolving the possibilities of Additive Manufacturing on scale, shape, and materials with HERON AM.
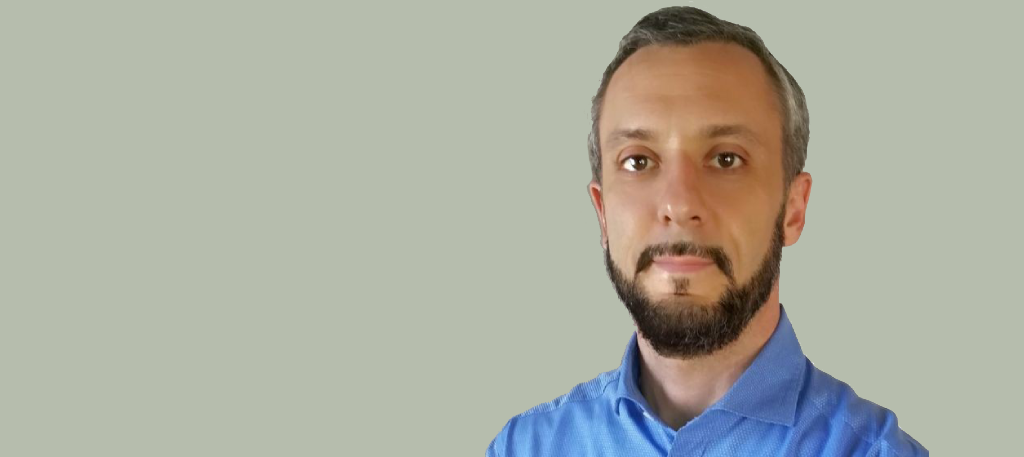
Why did your company decide to apply to the INTEGRADDE’s Expression of Interest Call?
Because it was a test-before-invest opportunity for us. It was in line with our need of exploring process in-situ monitoring architectures for our pilot DED system.
How is the process of applying and selection? Would you recommend it?
What services did you choose and why?
What would you say are the benefits your company has acquired from this experience?
- Increased know-how on sensors, h/w & s/w for in-situ process monitoring
- Shared experience in process monitoring and digital twin applied to WAAM
- Acceleration toward the development of an industrial in-process quality control system
Why do you thinkin the INTEGRADDE EOI experience is relevant for EU’s AM market?
A seamless digital integration of AM process in the product lifecycle is key to a wide adoption of AM at industrial level. The INTEGRADDE EOI experience demonstrated that open innovation can accelerate the digital integration.
Could you give us a testimonial about the involvement of your company as a INTEGRADDE EOI beneficiary?
How was the experience of your host Open Pilot Line?
It was a challenge to get everything ready to workshop in a short time but it worked thanks to the very good interaction between the teams and to the technology readiness of the solution. We made our robotic WAAM system available with some software and hardware adaptation to get ready to host the INTEGRADDE process monitoring system according to provided specifications. Everything went smoothly and in a few week we were able to end up with a successful integration test of the Pilot Line. We have been able to build up a basic process digital twin of demo part.
What problem did the service answer? Is it something you would recommend to other companies?
The final goal of a robust manufacturing process industrially accepted, that can be complex with DED technologies for AM, is to implement real-time control algorithms for a zero-defect manufacturing strategy. In order to achieve this goal a suited monitoring system is required. While achieving this complex task, the process monitoring and data acquisition systema can be very useful for:
- Early detection of defects
- Data analytics
- Process and product quality certification
I would recommend other companies to try the service because the ratio benefit/effort is efficient, though the provided solution still need more steps to get completed and industrialized.
What would you say are the lessons learnt from this experience?
- Standardization of machine communication protocols has come to a sufficiente level for real industry 4.0, though plug&play solutions still missing.
- Open innovation works especially when people from research and industry ‘’play’’ together on the same ground to make things work.
Would you consider your experience a success? If so, why?
Is your case replicable?
Is this a process you would recommend?
Yes