The institution’s mission to pioneer research in future production industries. Central to their efforts was the development of an open pilot line, showcasing a modular approach to production environments.
The interview underscored the significance of overcoming mindset barriers within companies to fully leverage cutting-edge solutions. Reif emphasized the potential benefits of embracing new concepts like digital product passports and sustainable manufacturing practices. Looking ahead, Smart Factory KL envisions a future where resilience and environmental consciousness drive production processes.
Solutions Implemented:
1. Advanced Manufacturing Consultancy: Leveraging Smart Factory Solutions for Printcirc’s Growth
Smart Factory KL provided consultancy services to Printcirc, a startup seeking guidance on integrating advanced manufacturing technologies into their operations. This service involved discussing the potential integration points of Smart Factory’s technologies, such as the open pilot line concept and asset administration shell technology, with Printcirc’s business model and production processes. The goal was to explore how these innovative solutions
could enhance Printcirc’s manufacturing capabilities and drive operational efficiency.
Key Insights
- 1. STRATEGIC ALIGNMENT
- 2. CONCEPTUAL EXPLORATION
- 3. POSITIVE RECEPTION
- 4. FOCUS ON REAL- WORLD APPLICATION
- 5. RECOMMENDATIONS
The collaboration involved in-depth discussions and explorations of Smart Factory’s technologies, such as the open pilot line concept and asset administration shell technology, to identify potential integration points with Printcirc’s operations.
This process allowed both parties to assess the feasibility and benefits of adopting these advanced manufacturing solutions.
Despite being in the early stages and not yet implementing the solutions, Printcirc showed keen interest and enthusiasm for Smart Factory’s concepts.
The initial exchange was constructive, with Printcirc expressing a desire to learn
more and explore further collaboration opportunities, indicating a promising start to the partnership.
Smart Factory emphasized the importance of translating research concepts into practical applications that address real-world challenges.
While the full implementation was pending, the collaboration focused on understanding Printcirc’s specific needs and how Smart Factory’s solutions could offer tangible benefits, laying the groundwork for future developments.
The key recommendation is to ensure continuous communication and collaboration between Smart Factory and Printcirc, fostering a tailored approach to solutions, ongoing knowledge sharing, and alignment with evolving needs for maximizing the benefits of their partnership.
Testimonial
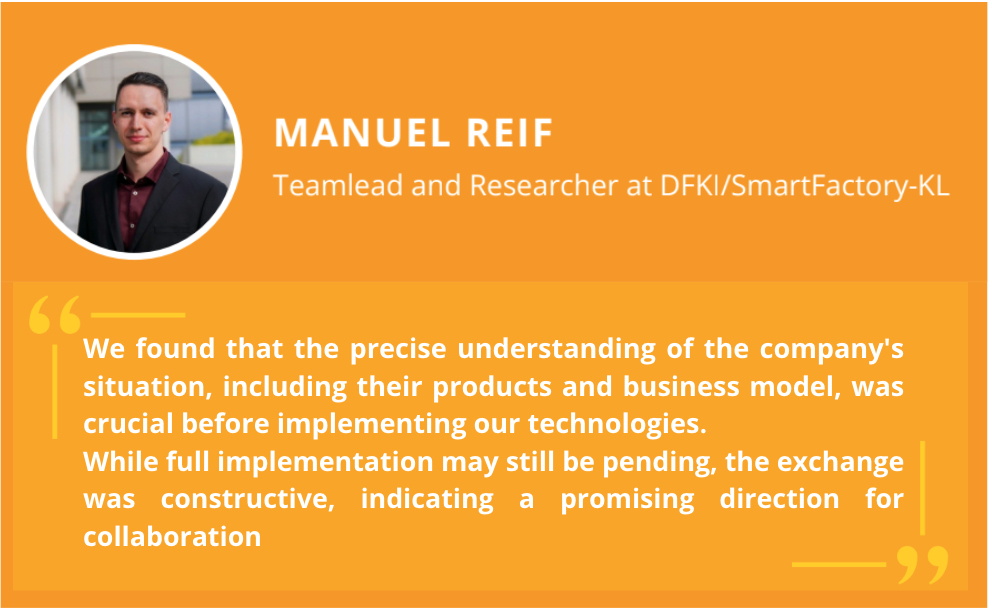
Takeaways
- Modular production and decentralized systems offer scalability and flexibility.
- Emphasizing open standards and technology integration enhances interoperability.
- Tailored consultancy services support navigating technological advancements.
- Overcoming adoption challenges requires mindset shifts towards innovation.
- Continuous collaboration ensures future readiness and adaptation to industry trends.
Project info:
The use case DIMOFAC project which received funding from the European Union’s Horizon 2020 research and innovation programme under grant agreement No 870092, aiming to help factories implement a smart factory architecture that will allow them to be more reactive to a personalised demand and changing market dynamics.