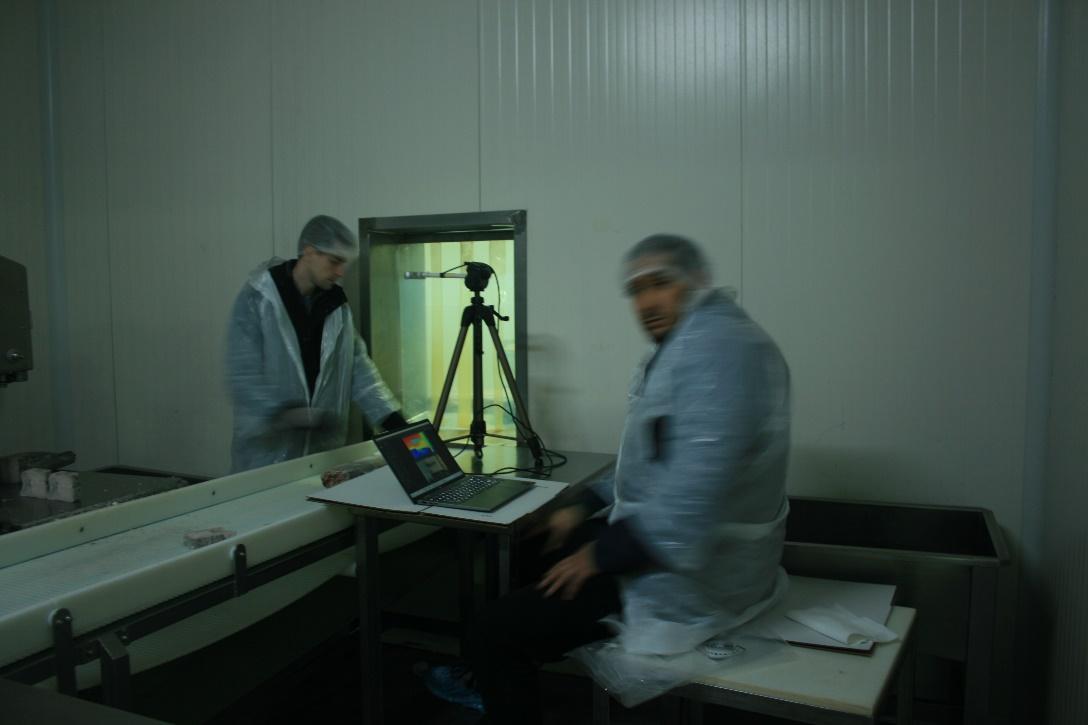
One of the objectives of the PRODUMAR pilot is to support its operators in classifying fish steaks to help separate them by category per box. To obtain this classification, annotated samples are needed to train the algorithm. Therefore, on March 2nd and 3rd, UNINOVA and FBK went to PRODUMAR to collect images of the fish for the Smart Sensing Suite.
Produmar was founded in 1975, pioneering the activity of preparing and freezing fish in the area in which it operates – Vila do Conde. In more than 30 years of activity, it is proud to have had the quality of its products as the main factor in its development, which is clearly evident in the market it supplies.
The UNINOVA Institute is a multidisciplinary, independent, and non-profit research institute employing around 150 persons, located in the metropolitan area of Lisbon.
Fondazione Bruno Kessler (FBK) is a multidisciplinary research institution specializing in the fields of technology, innovation, the humanities and social sciences, based in Trento.
FBK and UNINOVA are working collaboratively to develop technologies to improve PRODUMAR fishing production line. Specifically, they are working on a Smart Sensing Suite, whose main goal is to develop self-calibrating sensing solutions to grade the quality (both interior and exterior) of delicate objects and to produce a mesh of integrated and overlapping sensors that will improve production-line traceability, agility and reconfigurability.
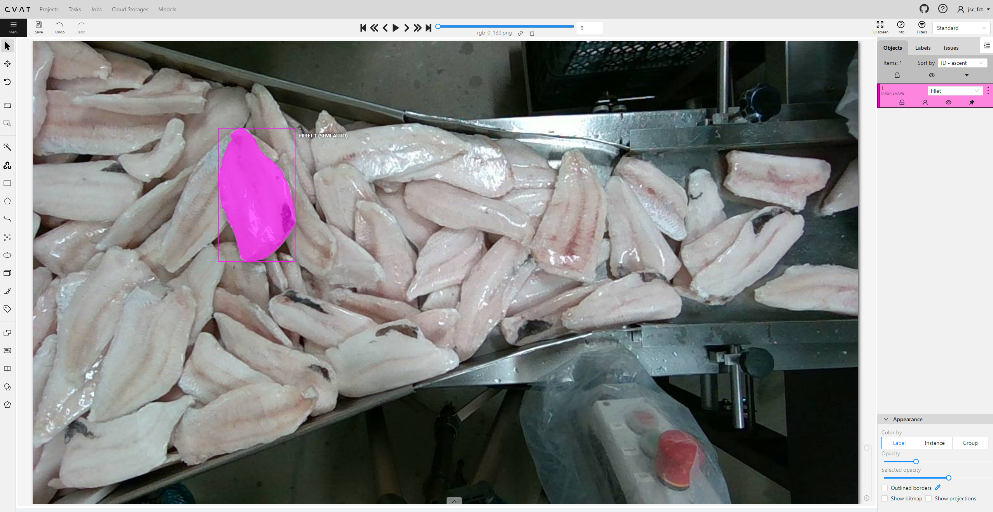
FBK and Uninova visit to PRODUMAR had four main objectives:
1) Verify the requirements for classifying fish, there are two types of classification based on the perimeter of the fish steak. The different fish steak types were demonstrated to understand the difference between the classification and to proceed to the next step, which is annotating the photos, and subsequent training of the algorithm.
2) Verify the condition of the fish cutting on the conveyor belt to identify where to place the camera and the quantity of light.
3) Testing the camera in production, it was decided to use an Intel RealSense D456 depth camera to capture fish steaks during the cutting phase. During these days, the camera was placed on the conveyor belt, so that we could check the working conditions and verify the quality of the photo. It was important that we were physically at the location, to check the amount of light and whether the camera support was adequate.
4) Collect image datasets, 200 images were collected per dataset. Datasets were obtained from 3 distinct phases (cutting, category and packaging). In the cutting phase, we obtained datasets from 2 different species and in the packaging and classification phases, we obtained 3 different datasets (posts A and B and fillets).
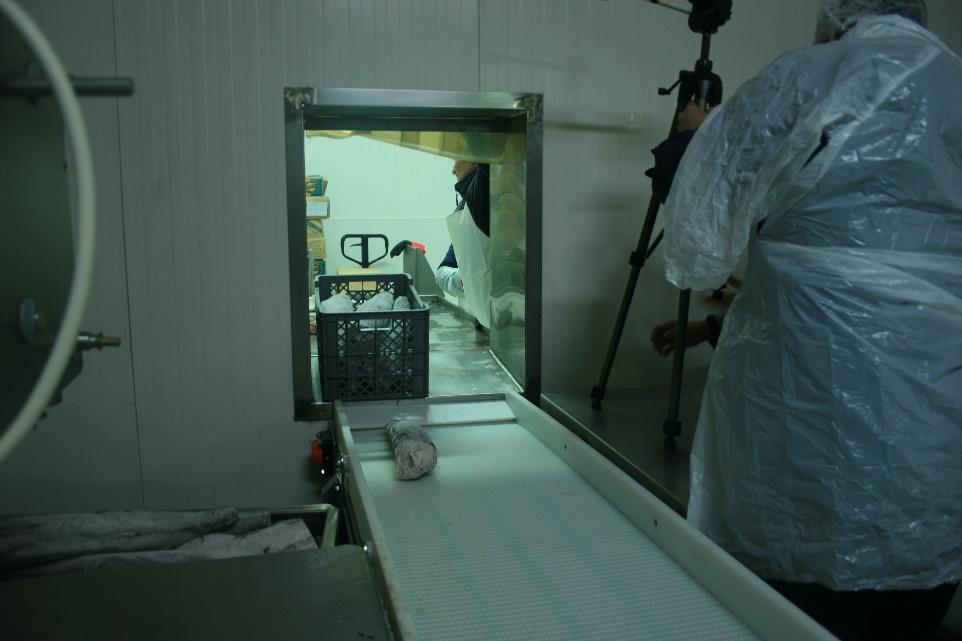
During this visit, they tested all the solutions from the “Smart Sensing” Suite:
- Grade the Quality: A cost-effective, accurate and fast solution to grade the quality (both interior and exterior) of delicate objects.
- Self-Calibrating: A self-calibrating solution for producing networks of
- sensors to improve production-line traceability.
- Data-Sets: Data-sets containing scans of delicate objects in a real environment with ground-truth data.
As an output of the visit to the PRODUMAR facilities, they collected all the datasets necessary for training the AI algorithm to identify the fish steaks. Identify in the fish production process where they could place sensors for traceability and placement of cameras. Finally, the space on the factory floor was also analyzed to identify the best positioning of the robotic arm.“
If you want to know more about the technologies they are testing and how you can be next to improve your production line in terms of self-calibration, and soft-handling products, join the AGILEHAND community in Discord and we’ll keep you updated.