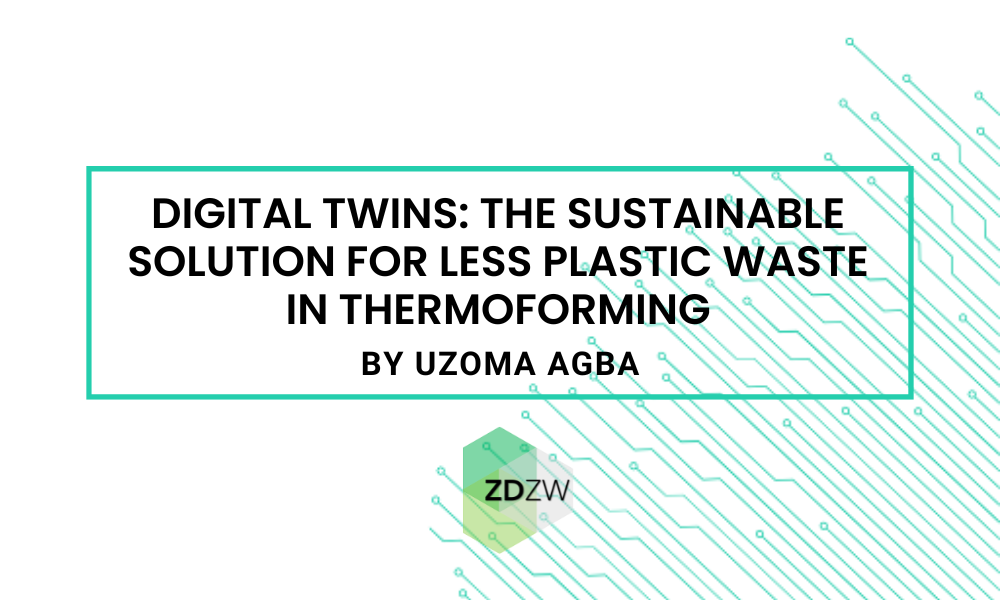
Digital Twins: The sustainable solution for less plastic waste in Thermoforming
Thermoforming is a vital part of countless manufacturing industries. It involves heating plastic sheets and molding them into specific shapes using molds. This process finds application across various industries, from creating packaging for consumer products to producing durable components for aerospace and medical devices. Despite its versatility, traditional thermoforming methods present challenges such as uneven wall thickness and limited capabilities in handling complex geometries.
More so, traditional methods in these manufacturing industries can be wasteful, using more plastic than necessary and leading to unnecessary downtime.
This is where a groundbreaking technology called “digital twins” steps in, offering a win-win for manufacturers and the environment. Engineers can create a virtual version of the mold and the entire production process with the digital twins’ technology. This allows them to test and tweak the design, minimising the amount of plastic needed while ensuring a perfect product. It is like having a practice round before the real game, except the game is saving precious resources.
Due to its viability, the digital twin market is poised for remarkable growth. According to Mordor Intelligence, it is estimated to be USD 26.14 billion in 2024 and projected to soar to USD 125.89 billion by 2029. This exponential rise highlights the transformative potential of digital twins in various industries, including thermoforming.
At the heart of this transformation lie advanced technologies such as the Internet of Things (IoT), cloud-based platforms, machine learning (ML), and artificial intelligence (AI). These innovations converge under the banner of Industry 4.0, driving the widespread adoption of digital twins across the manufacturing landscape.
Furthermore, one of the key advantages of digital twins lies in their ability to optimise design and production processes. By simulating thermoforming processes, engineers can fine-tune mold designs, minimising plastic usage without compromising performance. Moreover, traditional methods, reliant on trial and error, are eclipsed by the precision and efficiency of digital twins. From the first Industrial Revolution to the current era of Industry 4.0, each phase has brought innovations reshaping the manufacturing ecosystem. The focus has now shifted towards digitalisation, artificial intelligence, and data analytics, enabling a tighter connection between the physical and virtual realms.
Additionally, digital twins offer insights beyond mere design optimisation. They enable manufacturers to identify production bottlenecks, streamline operations, and preemptively address equipment malfunctions. This proactive approach not only minimizes downtime but also maximizes overall efficiency, contributing to sustainable manufacturing practices.
The significance of digital twins also extends to the realm of sustainability. By analysing the entire lifecycle of plastic products, from production to disposal, it helps manufacturers identify opportunities for recycling and reuse. This holistic perspective empowers them to design products with reduced environmental impact, aligning with global sustainability goals.
Despite their immense potential, the widespread adoption of digital twins faces challenges, particularly in underdeveloped regions with legacy systems. These systems, lacking connectivity and real-time data capabilities, hinder the integration of advanced technologies. However, the COVID-19 pandemic has catalysed the adoption of Industry 4.0 solutions, propelling the digital twin market forward.
Governments worldwide are also embracing digitalisation initiatives to enhance urban resilience. For instance, Singapore is spearheading efforts to accelerate digital transformation across industries, signalling a global shift towards smart manufacturing practices.
In the relentless pursuit of sustainable manufacturing, the Zero Defect, Zero Waste (ZDZW) initiative emerges, offering a comprehensive framework to minimise defects and waste throughout the manufacturing process.
Zero Defect, Zero Waste (ZDZW): A paradigm shift in thermoforming
The ZDZW initiative, funded by the European Union, aims to minimise defects and waste in manufacturing processes, thereby optimizing efficiency and reducing environmental impact.
In the context of thermoforming, ZDZW represents a paradigm shift, where every aspect of the process is optimised to achieve maximum quality and minimal waste.
The ZDZW framework
The ZDZW framework encompasses three key areas: defect minimization, waste reduction, and process optimization. These pillars work in harmony to address the entire manufacturing process and product lifecycle, ensuring that every stage is optimized for maximum efficiency and minimal waste generation.
Defect Minimisation:
One of the primary goals of ZDZW is to minimise defects in the manufacturing process. This involves identifying potential sources of defects, such as material inconsistencies or process variations, and implementing measures to mitigate them. By utilising advanced technologies like thermal inspection equipment and AI models based on Finite Elements Analysis (FEA), manufacturers can effectively control process variability and reduce the risk of defects.
Waste reduction:
In addition to defect minimisation, ZDZW also focuses on reducing waste generated during the manufacturing process. This includes material waste, energy consumption, and financial costs associated with scrap disposal. Through the implementation of non-destructive inspection (NDT) techniques and real-time process parameter control, manufacturers can significantly reduce waste generation and improve overall sustainability.
Process optimisation:
Central to the ZDZW framework is the optimisation of the thermoforming process itself. By leveraging advanced technologies like digital twins and AI-enhanced thermal imaging, manufacturers can gain valuable insights into process parameters and performance. This enables them to make real-time adjustments to optimize efficiency, minimize waste, and ensure consistent product quality.
The ZDZW Impact on KPIs
The impact of ZDZW on key performance indicators (KPIs) is profound. By reducing raw material usage and scrap ratio, manufacturers can achieve significant cost savings and improve overall equipment effectiveness. For example, a 0.6mm reduction in material thickness per sheet can lead to substantial material savings, while a 3.5% decrease in scrap ratio can result in thousands of parts saved per year.
Addressing sustainability challenges in Thermoforming:
As awareness grows about the environmental impacts of manufacturing, so does the focus on reducing material use and waste. In light of this, initiatives like the UN’s Sustainable Development Goals and the EU’s Green New Deal emphasise the need to cut carbon footprints and resource consumption. To meet these goals, manufacturers must find innovative ways to boost efficiency and reduce waste.
The use case digital twins in thermoforming:
Enterprises like Arçelik, a leading Turkish durable goods manufacturer, are embracing digital twin technology to revolutionise their production processes. Collaborating with Simularge, a pioneering Digital Twin Startup, Arçelik started the journey to enhance sustainability in its refrigerator production line. Focusing on thermoforming—a critical stage in manufacturing inner plastic parts—the aim was to optimise processes and minimize defects and waste generation.
Implementation and results:
The journey began with an analysis of process characteristics, parameters, and challenges, laying the foundation for the development of a robust digital twin model.
Leveraging sensor data and PLC technology, the team integrated real-time production insights with advanced finite element simulations. The implementation yielded remarkable results, with a 50 per cent reduction in scrap ratio and a 10 per cent decrease in raw material consumption, translating to annual savings of USD 2 million.
Sustainable production:
Beyond the financial benefits, the adoption of digital twins has far-reaching implications for sustainable production. Manufacturers can align with global sustainability goals while improving operational efficiency by optimising processes and enhancing product quality. Similarly, collaboration and data accessibility emerge as key enablers, facilitating the seamless integration of digital technologies into the manufacturing landscape.
Thermoforming: Shaping the future of manufacturing
Thermoforming is a multifaceted manufacturing process that blends innovation and tradition in modern industry. It involves shaping heated plastic sheets using various methods, providing manufacturers with a diverse toolkit to realize their designs. Vacuum forming and pressure molding are among the various techniques in thermoforming, known for their efficiency and cost-effectiveness.
- Vacuum Forming:
This method uses negative pressure to mold plastic sheets. After heating the plastic, a vacuum-forming machine extracts air to press the sheet onto a mold. It’s known for its cost-effectiveness and speed.
- Pressure Molding:
Involves heating plastic sheets and pressing them against a mold using vacuum and pressure. This process enhances the plastic’s ability to retain its final shape, ideal for detailed parts.
- Mechanical forming:
Direct mechanical force is applied to shape heated plastic sheets. Using a core plug, the flexible sheet is pressed between the plug and the mold, ensuring precise detailing.
- Overlay molding:
Heated plastic sheets are placed over a patterned mold, pressing the pattern into the plastic to form the part. This is a cost-effective method that maintains material thickness, creating sturdy parts.
- Positive-negative forming:
For precision parts, this method uses positive and negative molds to shape the plastic sheet. The molds compress the sheet to match their contours, ensuring high precision.
- Twin Sheet process:
Involves forming two plastic sheets simultaneously, then joining them to create a single piece. Ideal for parts with cavities or double walls.
- Blowing:
This technique shapes heated plastic without molds by blowing compressed air into the plastic until the desired shape is achieved.
Choosing thermoforming equipment:
Choosing the right thermoforming equipment is crucial, considering factors like molding surface, draw depth, equipment dimensions, clamping force, and tool change options. Thermoforming equipment comes in various types, including industrial devices for high production volumes, desktop thermoformers for prototyping, and homemade options for DIY enthusiasts.
Types of Thermoforming Equipment:
- Industrial Thermoforming Devices: For medium to high production volumes, offering compatibility with various materials and strong vacuum forces or pressure. Costs start at $10,000.
- Desktop Thermoformers: Smaller, used for prototyping and small-batch production. Prices start under $1,000.
- Homemade Thermoforming Equipment: DIY option for experimentation, requiring specialist knowledge.
Using 3D Printing for Thermoforming Tools:
Traditional mold manufacturing can be costly and time-consuming. To streamline the thermoforming process, many companies are turning to stereolithography 3D printing (SLA) for rapid tooling. SLA printers like the Form 3+ and Form 3L offer speed, cost efficiency, expanded material options, and ease of use, revolutionizing thermoforming processes.
This innovative approach enables manufacturers to create complex molds with intricate designs quickly and affordably, opening new possibilities for customization and efficiency in plastic manufacturing.
As technology continues to evolve, so does the world of thermoforming. From traditional vacuum forming to cutting-edge twin-sheet processes, manufacturers have a plethora of options to choose from. Industrial thermoforming devices offer high-volume production capabilities, while desktop thermoformers cater to prototyping and customization needs. Moreover, the advent of homemade thermoforming equipment opens new avenues for experimentation and innovation.
Conclusion: Sustainable manufacturing future through digital twins technology
The integration of digital twins into manufacturing brings forth advanced inspection techniques, while 3D printing ushers in a new era of efficiency and sustainability. Embracing these technologies will enable manufacturers to realize the vision of zero defects and zero waste, paving the way for a brighter and more sustainable future.
Expected impacts of implementing ZDZW techniques in Thermoforming:
The ZDZW platform plans to incorporate 100 per cent thermal inspection equipment in the thermoforming process to prevent quality failures due to variability.
- Real-time measurement of inner body thickness:
The first step involves real-time measurement of the inner body thickness to ensure uniformity and quality.
- Testing and deployment of FEA-based AI model:
The second step focuses on testing and implementing a Finite Element Analysis (FEA)-based AI model in the production line under various conditions. This will enhance predictive maintenance and improve overall process efficiency.
- Scrap detection and KPI tracking:
The third step includes scrap detection using image processing techniques and the tracking of KPIs to ensure continuous improvement in the manufacturing process. The ZDZW initiative is poised to transform thermoforming by fostering a culture of quality, efficiency, and sustainability.