In-line quality assurance modules
Smart, adaptive and seamless quality assurance for laser manufacturing
Project: R3GROUP
Publisher: AIMEN
Technology: Additive Manufacturing
Industry: Manufacturing, Automotive, Industry
INTRODUCTION
The IR-based monitoring and control system ensures component quality in reconfigurable laser cell processes by using machine learning to correlate infrared (IR) images with experimental data from destructive and non-destructive tests. This reduces reliance on randomized controlled testing while ensuring compliance with quality standards.
With real-time monitoring and adaptive defect prevention, the system enhances precision beyond traditional quality control. Its multipurpose laser head minimises tooling investments, offering a cost-effective solution. Proven in laser beam welding for automotive parts, it has achieved a 92% positive defect classification rate.
By integrating machine learning and advanced laser technology, this system transforms in-line quality assurance, delivering high performance and efficiency in manufacturing.
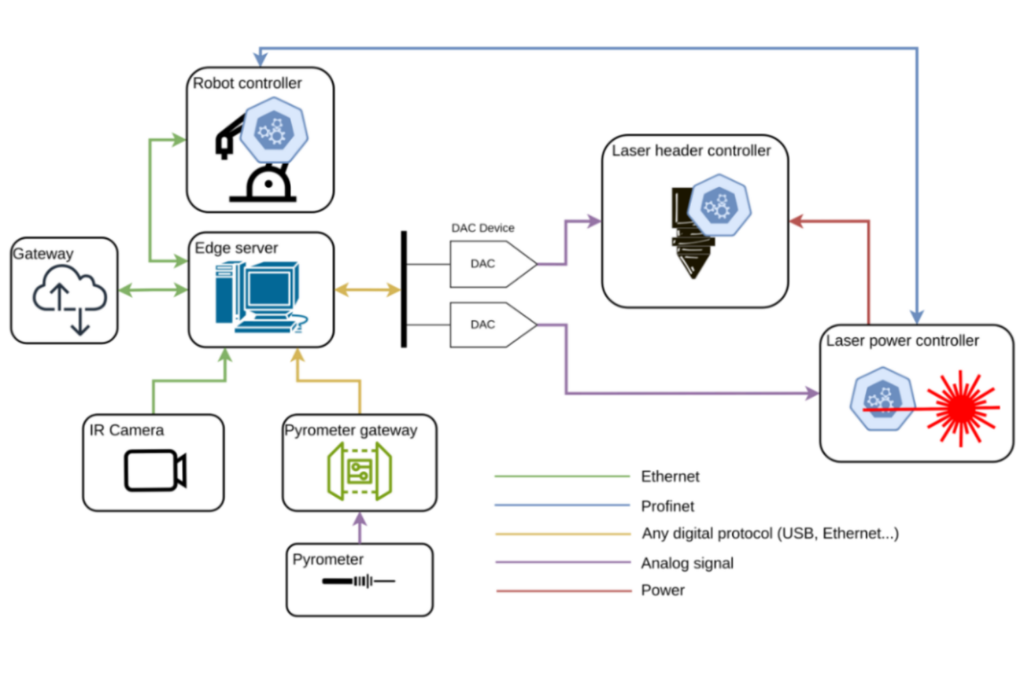
FEATURES/BENEFITS
The main benefits of this solution are:
- Near-zero material waste and rejected pieces by ensuring 100% production quality.
- Reduced randomized testing and greater manufacturing flexibility with a single toolset.
- Faster response to continuous defects, identifying tooling or equipment failures early.
- Full in-line quality control with 100% traceability through linked part ID monitoring.
TECHNICAL INFORMATION
The main features of this solution are:
- Sensor setup for real-time monitoring of laser processes, communicating with the robot and laser power.
- Adaptive IR-based control to ensure process accuracy, reducing material waste and execution time.
- Inline quality control using machine learning and destructive test data to verify 100% of production.
- Advanced system modelling (AAS) to track the digital thread of manufactured components.