The food industry needs resilience technologies as their products often face different sizes and needs. That’s why the AGILEHAND project is developing advanced technologies for grading, handling and packaging autonomously soft and deformable products, as a strategic instrument to improve the flexibility, agility and reconfigurability of production and logistic systems of the European manufacturing companies.
These new technologies are being tested in real scenarios to understand their applications in different setups and to adapted to the market needs. One of those companies that are testing these solutions is MARELEC, a food manufacturer in Belgium that is working as a pilot company. They specialises in intelligent portioning, customized weighing, grading solutions, trimming and inspection.
Resilience technologies for flexible Food processing: MARELEC contribution in AGILEHAND initiative
MARELEC serves the poultry, meat, seafood, and marine sectors, designing and producing innovative turnkey systems that deliver high-quality output and maximum yield for food processors worldwide. With over 40 years of experience, MARELEC is recognized globally as a high-tech solutions provider for secondary food processing.
Their team of engineers and industry experts follows a customer-driven design approach, using advanced technologies such as portioning software with intelligent cutting algorithms. These systems are designed for high speed and precision, helping operators maximize yields and maintain the highest quality standards.
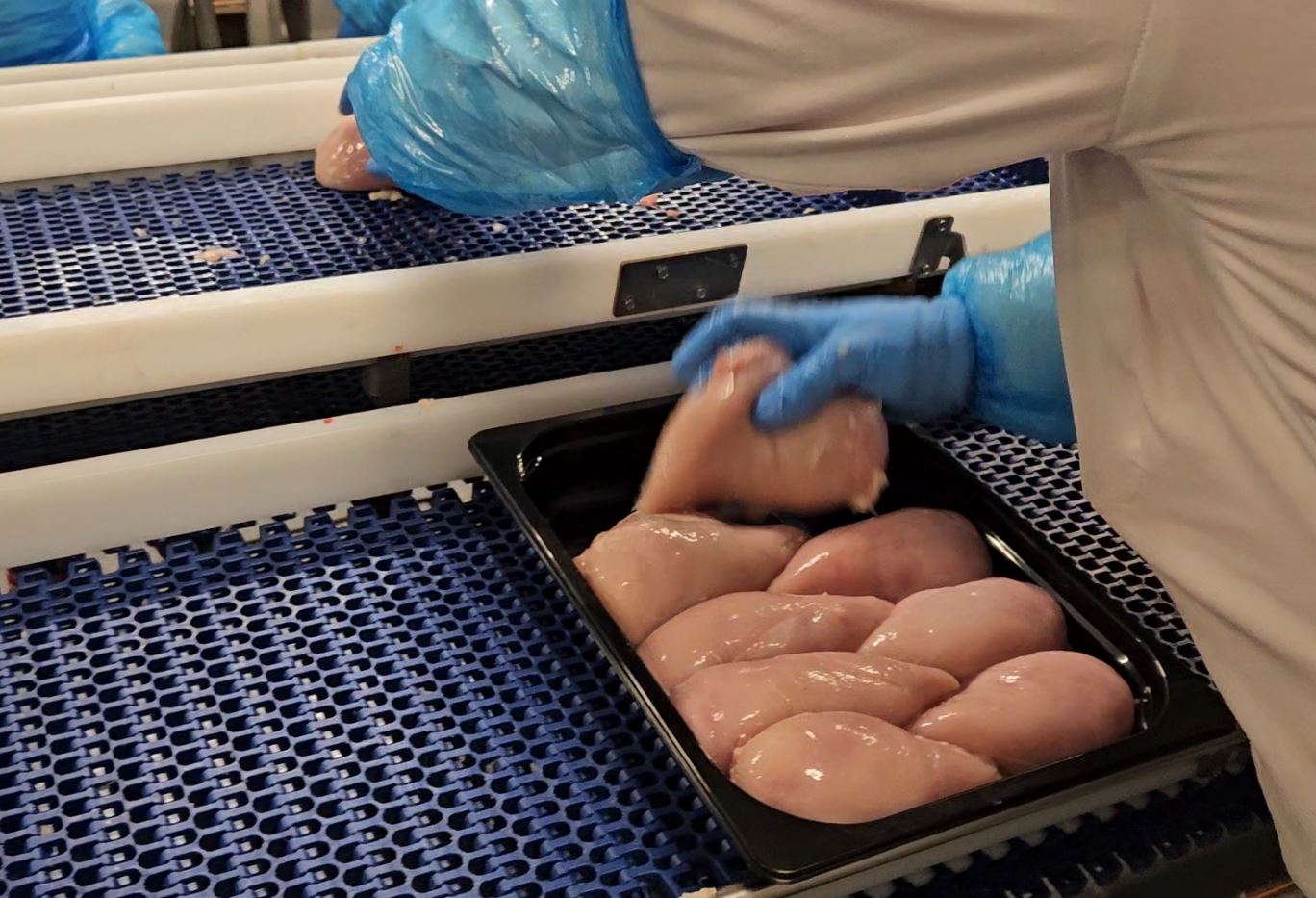
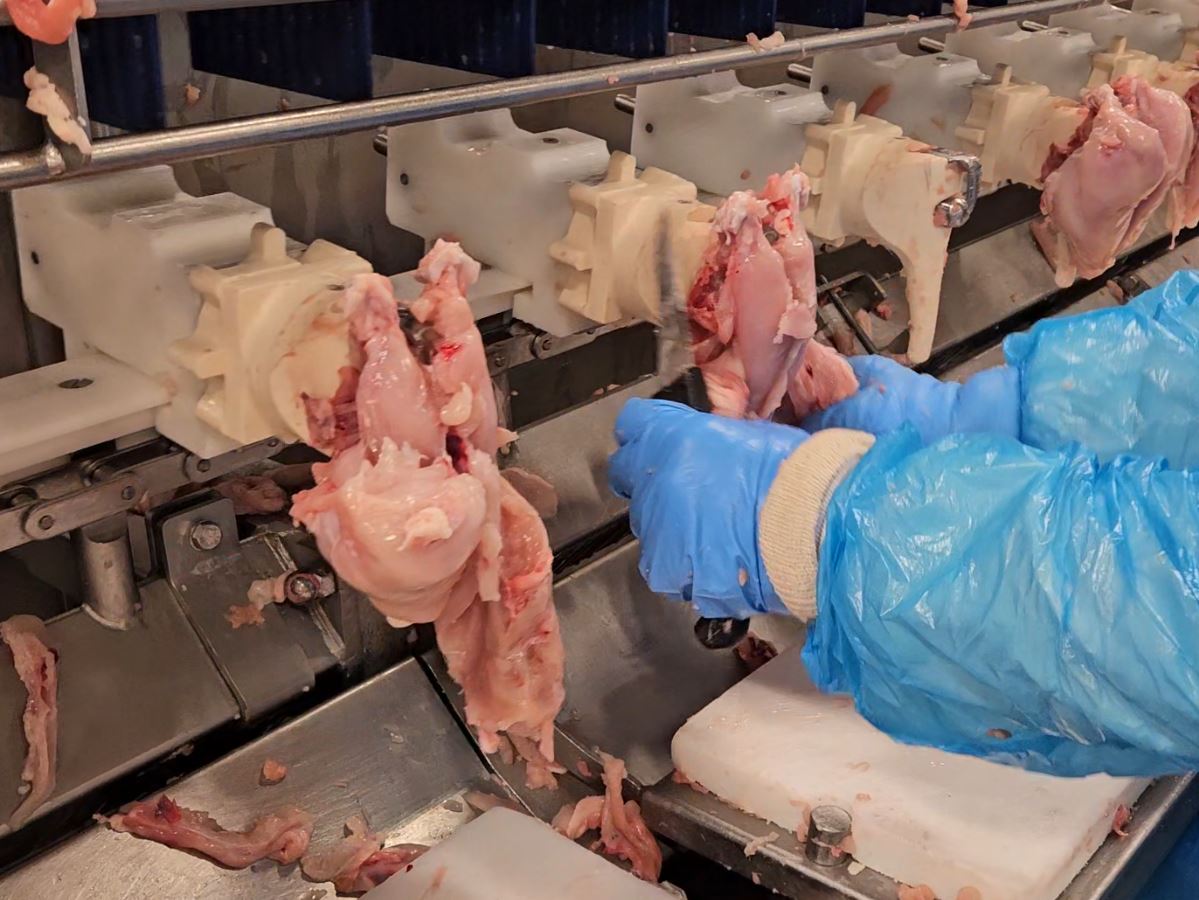
The primary goals of the AGILEHAND pilot at MARELEC are to enhance the efficiency, accuracy, and flexibility of their handling and packing operations. This includes:
- Reducing human error by implementing advanced algorithms for intelligent portioning, grading and objective quality assessment.
- Minimizing operator injuries by automating hazardous tasks within harsh working environments.
- Improving product quality through a more precise and objective way for grading and carefully handling the soft deformable goods without damaging them in the process.
Within the MARELEC pilot case, they will use different technologies according to the requirements. For grading and agile rapid configuration, Artificial Intelligence is used in our advanced grading algorithm. These algorithms assess the internal quality of the chicken fillets, leading to more accurate grading and sorting. In combination with our intelligent portioning machine, these algorithms scan chicken fillets before cutting them to the desired weight, ensuring uniformity and reducing waste. Using a Digital Twin setup of the entire production process, multiple production runs can be simulated to determine the optimal grader settings and prioritize order items. This provides the production manager with an optimized forecast for the next days production planning, helping to maximize yield from the available raw materials while meeting predefined delivery schedules and required order quantities.
Combined grading and packaging systems offer an automated solution for efficiently handling and processing deformable products.
By running real-time simulations based on feedback from the actual raw materials supplied, the production manager receives actionable suggestions to adjust the production process accordingly. Combined grading and packing systems offer an automated solution for handling chicken fillets, eliminating the need for operators to manually pick, place, and arrange the fillets in packaging. Since this task is repetitive and performed in harsh working conditions, the AgileHand solutions, with robots and cobots, provides an ideal automation alternative.
This reduces the risk of operator injuries and illness associated with repetitive work. The new system is designed to quickly adapt to different packaging needs for chicken fillets through the use of a Digital Twin. This allows for real-time simulation and adjustments based on historical and current data, enabling swift changes in the production process. Advantages to the production process are:
- Enhanced flexibility: the ability to rapidly switch between different product types and packaging requirements makes the production process more versatile.
- Reduced downtime: quick reconfiguration means less time is spent on changing setups, leading to continuous production flow.
- Improved efficiency: streamlined processes and reduced manual intervention lead to faster and more accurate handling and packaging.
The expected benefits from implementing the AGILEHAND solutions are:
- Increased efficiency: Faster and more accurate sorting and packing processes.
- Cost reduction: Lower grading and energy per squared meter costs due to automation in a compacter footprint and reduced waste by a correct quality assessment which results in a bigger yield of the raw material.
- Quality improvement: an objective product quality assessment which leads in a precise grading and gentle handling of the deformable product on a reduced footprint, leading into fewer damaged goods and longer shelf life and more precise expiry date to indicate on the packaging label.
The collaboration between AGILEHAND developers partners and MARELEC represents a leap forward in the application of advanced technologies within the food industry. By integrating intelligent portioning, grading, and automated handling systems, this pilot project showcases how cutting-edge solutions can transform traditional manufacturing processes into more efficient, flexible, and sustainable operations.
Stay tuned for more updates on how AGILEHAND technologies are revolutionizing production systems and reshaping the future of manufacturing!